 |
|
Topic: Bulk import of BOM/Sub Assemblies
|
By: Colin Foster | Posted on: Feb 9 2023 at 07:41:57 AM | Trying out miniMRP on behalf of a client.
We have an Excel workbook that has lists of Part numbers (with prices, etc) & I've been able to save that as a CSV & upload into miniMRP.
However, we also have a large number of Sub-Assemblies with details of the part nunbers (& quantities) that are needed for each S-A/BoM... is there a way that these could be imported as a bulk file. At the moment, it would appear that they have to be imported Sub Assembly at a time which will take quite a while | |
By: Guest#99 | Posted on: Feb 9 2023 at 08:19:03 AM | If you're using v5 then you should be able to import a multi-level BOM.
Look at this picture.
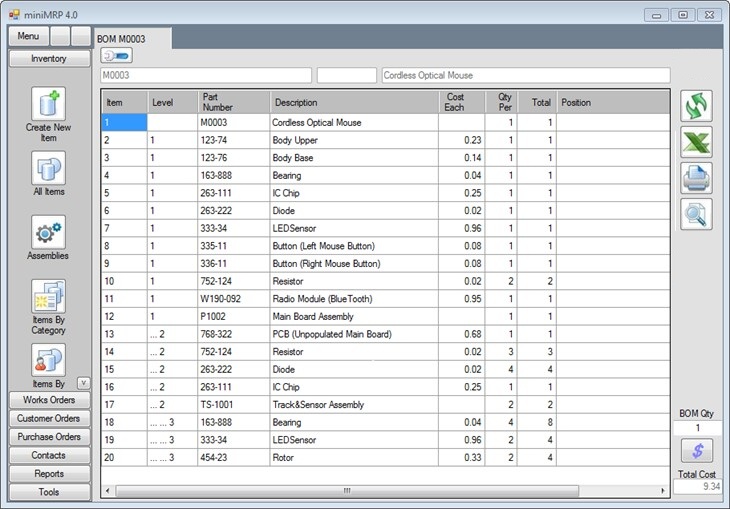
If the layout in your CSV is like this with a "Level" column then you can import it.you can import it. | |
By: Guest#99 | Posted on: Feb 9 2023 at 08:24:52 AM | I forgot to say. That picture in my previous post is not the import process. It's just how minimrp displays a multilevel BOM. I'd say that that is a common industry standard way to show a multi level BOM. That level column has dots ... to indent the level number. But in your csv it doesn't matter if you have dots, spaces or tabs or nothing. Just the numbers.
during the import process I imagine minimrp is just stepping down the list one row at a time and when it sees the step from level 1 to 2 and then 2 to 3 it knows that it's dealing with sub assemblies.
Make a backup. Then have a play. You can then make mistakes and just restore and go back and try again. | |
By: Colin Foster | Posted on: Feb 9 2023 at 08:50:28 AM | Hi,
Thanks for that, so just need to add the column for levels, then... cool (I hope :-) )
Yes, trial & error worked when I imported basic parts details!
Will try this out, cheers | |
By: Colin Foster | Posted on: Feb 9 2023 at 09:57:53 AM | Further thought...
We have various sub-assemblies for the constituent parts of a timber building - Roof (different types), End Bays, Intermediate Bays depending on the "main product" these will be different. But, presumably, once created, I'd be able to use an existing sub-assembly as part of another, unique building).
Also, Building type A can have a steel roof OR a fibre cement roof OR a plastic roof... presumably when creating the "Main BOM", I would include each of these & then, if I need a costing of a Building type A, I call it up off teh system & if it needs a steel roof, I say one of those & zero fibre cement or plastic roofs? | |
By: Support | Posted on: Feb 10 2023 at 06:56:40 AM | If you have a BOM for "BuildingType_A" which has a steel roof and you decide you want to make a similar building but with a plastic roof then I would suggest creating a whole new building type. "BuildingType_B".
To create that type B you don't need to key everything in again. Just open the BOM for type 'A' into the parts list editor and then 'SaveAs' with a new name "BuildingType_B". That will create a whole new parts list that you can edit - ie delete the sub assy for the steel roof and insert the sub assy for the plastic one.
Now you have two totally separate product assemblies.
The reason I recommend having totally different assemblies that if you created a work order to build one with a steel roof and then also wanted to build one with a plastic roof you'll just confuse everyone who goes back to look at the BOMs.
In fact, once you'd sold a BuildingType_A you should never go back and change its BOM. If you need to make a slight variation to type A just create anothe type A but with a different revision number.
But in the end you can do it your way too but I can't recommend it.
| |
By: Colin Foster | Posted on: Feb 11 2023 at 01:33:53 PM | Hi,
Thanks for that - makes a lot more sense - both in terms of new buildings (type A vs B) and "tweaks" (we now need an extra widgit"
| |
By: Colin Foster | Posted on: Feb 12 2023 at 03:03:29 PM | OK, so I'm obviously doing something wrong...
Saved a second building type - decided that this needed 3 interior bays, so changed quantity of the relevant bay to be told that if these are standard assemblies, then the changes will apply to all assemblies that use these sub assemblies - but it's only this building that I want to have 3 internal bays.
So then tried again, creating another new building type with the key sub assemblies included 3 times, which does seem to be crazy.
Made the decision that wasn't working (& I've not, yet - or at least obviously - been able to generate a completed "set" of a new building in stock.
So decided to try from a different angle - created a customer order made up of a number of sub assemblies (including telling the system that I need 3 of the interior bays).
That's fine, but then I'm unable to do anything with them! I can't create a works order (as shown in the online help) as the options given for v4.0 appear to be different in the 5.0 version that I'm testing.
So, conclusions are...
1. Perhaps I've set up sub assemblies incorrectly - but they look like the screenshot above
2. I'm missing/not understanding a step (highly likely!)
3. I'm trying to use the system outside of what it's designed to do (don't think so)
Any help would be appreciated! | |
By: Support | Posted on: Feb 15 2023 at 07:32:09 AM | You say there's a difference between the way v4 handled work order. I'm not aware of any breaking changes between the versions. v5 may have additional options but the basic work order should be the same.
If I've understood correctly you have a MultiLevel parent assembly and you want to go into that parent assembly and make a change to a sub assembly and you want that change to only affect the one parent you're working with. (v4 wouldn't let you do that either)
If you have a sub assembly and you make a change to that sub assembly then that change will affect that sub assembly wherever it appears.
As an example go back up and look at the picture I posted. See that sub assembly "TS-1001" "Track&SensorAssembly". If I went into a top level product where that subassembly is used and I switched out one component in that sub assembly then I've made a change to the "TS-1001" sub assembly and that will affect every other parent assembly that ever uses "TS-1001". This is not a bug. It's intentional. That sub assembly might be very common used in dozens of different products. If you improve the sub assembly then you'll want that improvement to be reflected in every product where that sub assembly is used.
We have to do that otherwise we'd have two different sib assemblies with different components but with identical part numbers.
Your post mentioned three conclusions. I think you have a combination of all 3. You're coming from excel work books where you're allowed to edit anything any way you want where a sub assembly can appear in multiple excel workbooks and you can edit one of them without affecting everything else.
It's possible that the way you work needs you to stick with the excel workbooks.
| |
By: Colin Foster | Posted on: Feb 24 2023 at 03:58:55 AM | Thanks for the response - the v4/v5 comment was more about what you see on screen (or that's how it appeared to look to me).
I also get the idea (having thought about it more) the logic that if you're changing a sub assembly, then that needs to be for a good reason & so it needs to flow through all uses of that S/a
But then, having done further "playing" I realised that my "Conclusion 1" above was the answer!! :-)
I'd set up a complete building as an assembly, with all of the various sub-assemblies... so, what this means is that I can create a building which comes with, e.g, a Fibre cement roof AND a steel one - no rain is going to come into my building!!
Rookie error!
So, deleted those sub assemblies & re-uploaded based upon the lower level (i.e. a Fibre Cement roof sub assembly & a steel roof sub assembly). Then, I can create the basic "standard" building by creating a new assembly & adding in the various relevant sub assemblies. But this also means that if we have to build a "one off", we just add the necessary s/a and, because we've created this as a new assembly, should someone else come along & want their own bespoke building (which turns out to be one that we've already created) then we can easily do that.
And yes, coming from Excel workbooks with their inherrent flexibility to a more structured system is constraining, however, that's what the business needs to do, so that the focus is on trying to reduce variations & therefore increase efficiency. Moving to a more structured Excel workbook from a completely free-typed one was a big change & in effect, a step towards looking at a product such as MiniMRP
Got a meeting with the client today to take him through the process, so we shall see.
Cheers | |
By: Colin Foster | Posted on: Feb 24 2023 at 03:58:57 AM | Thanks for the response - the v4/v5 comment was more about what you see on screen (or that's how it appeared to look to me).
I also get the idea (having thought about it more) the logic that if you're changing a sub assembly, then that needs to be for a good reason & so it needs to flow through all uses of that S/a
But then, having done further "playing" I realised that my "Conclusion 1" above was the answer!! :-)
I'd set up a complete building as an assembly, with all of the various sub-assemblies... so, what this means is that I can create a building which comes with, e.g, a Fibre cement roof AND a steel one - no rain is going to come into my building!!
Rookie error!
So, deleted those sub assemblies & re-uploaded based upon the lower level (i.e. a Fibre Cement roof sub assembly & a steel roof sub assembly). Then, I can create the basic "standard" building by creating a new assembly & adding in the various relevant sub assemblies. But this also means that if we have to build a "one off", we just add the necessary s/a and, because we've created this as a new assembly, should someone else come along & want their own bespoke building (which turns out to be one that we've already created) then we can easily do that.
And yes, coming from Excel workbooks with their inherrent flexibility to a more structured system is constraining, however, that's what the business needs to do, so that the focus is on trying to reduce variations & therefore increase efficiency. Moving to a more structured Excel workbook from a completely free-typed one was a big change & in effect, a step towards looking at a product such as MiniMRP
Got a meeting with the client today to take him through the process, so we shall see.
Cheers | |
Reply - add a comment to this topic.
You may enter letters, numbers and standard punctuation only. HTML and other scripts/tags will be rejected.
|
|
|